Oberösterreich: 5,68 Mio. Euro für massiven digitalen Innovationsschub für oö. Betriebe
Pressekonferenz mit Forschungsreferent LH-Stv. Dr. Michael Strugl, Mag.a Dr.in Henrietta Egerth (Geschäftsführerin FFG - Österreichische Forschungsförderungsgesellschaft), Dl Dr. Gerhard Dimmler (Leiter Forschung und Entwicklung, ENGEL AUSTRIA GmbH) und Martin Schwaiger (GF SATIAMO GmbH)
V.l.: Martin Schwaiger (GF SATIAMO GmbH), Mag.a Dr.in Henrietta Egerth (Geschäftsführerin FFG - Österreichische Forschungsförderungsgesellschaft), Forschungsreferent LH-Stv. Dr. Michael Strugl und Dl Dr. Gerhard Dimmler (Leiter Forschung und Entwicklung, ENGEL AUSTRIA GmbH). Foto-Credit: Land OÖ / Sabrina Liedl, Abdruck honorarfrei
Linz - Um dem Digitalen Wandel in OÖ weiteren Schwung und Auftrieb zu verleihen, fördert das Land OÖ 14 innovative Forschungsprojekte im Bereich der Digitalisierung mit einem Gesamtfördervolumen von insgesamt 5,68 Mio. Euro. Um Unternehmen mit unterschiedlichem digitalen Reifegrad gleichermaßen zu unterstützen, umfasste die Ausschreibung zwei Schwerpunkte:
(1) ‚DigiFIT‘soll Industriebetrieben den Start in Richtung Digitalisierung und einen raschen Anschluss im Digitalen Wandel erleichtern.
(2) ‚DigiVALUE‘soll Unternehmen mit fortgeschrittenem Automatisierungsgrad eine bessere und wertschöpfende Nutzung ihrer Daten erlauben.
Insgesamt wurden 20 Projektanträge eingereicht. Davon haben sich 14 Entwicklungsvorhaben vor einer internationalen Fachjury behauptet. 1,26 Mio. Euro Fördermittel wurden insgesamt an 4 Projekte im Bereich ‚DigiFIT‘ vergeben und 10 Projekte werden mit 4,42 Mio. Euro im Bereich ‚DigiVALUE‘ gefördert.
An allen Projekten sind jeweils Organisationen aus Wissenschaft und Wirtschaft beteiligt. Darunter sind wesentliche Key-Player des OÖ Innovationssystems vertreten – wie die FH OÖ Forschungs & Entwicklungs GmbH, die Johannes Kepler Universität Linz sowie außeruniversitäre Forschungseinrichtungen wie die RISC Software GmbH, die Software Competence Center Hagenberg GmbH und die Research Center for Non Destructive Testing GmbH, die zu den Forschungsbeteiligungen der Upper Austrian Research GmbH, der Forschungsleitgesellschaft des Landes OÖ, zählen. Im Rahmen dieser kooperativen Entwicklungsvorhaben arbeiten diese Forschungsorganisationen eng mit insgesamt 27 Unternehmen zusammen. Dass Digitalisierung und Industrie 4.0 nicht nur große Industriebetriebe betrifft, sondern auch ein zentrales Thema für den Klein- und Mittelstand ist, zeigt sich an derhohen Beteiligung von KMU-Betrieben. Insgesamt sind 15 innovative Klein- und Mittelbetriebe an den Projekten beteiligt, die rund 2/3 der Fördermittel im Unternehmensbereich einholen konnten. Einen großen Erfolg kann insbesondere die FH OÖ Entwicklungs & Forschungs GmbH verzeichnen, die 6 Projekte leitet, an weiteren 3 Entwicklungsvorhaben beteiligt ist und insgesamt 1,78 Mio. Euro Fördermittel einholen konnte.
Wirtschafts- und ForschungsreferentLH-Stv. Dr. Michael STRUGL
Die Digitale Transformation aktiv gestalten
„Der Digitale Wandel bringt enorme Chancen für den Wirtschafts- und Innovationsstandort OÖ. Die Digitale Transformation ist für Unternehmen eine Reise und nicht alle Betriebe starten von der gleichen Ausgangssituation. Einerseits finden sich viele Unternehmen mit stark ausgeprägtem Automatisierungsgrad und einer soliden Digitalisierungsstrategie bzw. Roadmap. Andererseits stehen viele Unternehmen noch ganz am Anfang ihrer Digitalisierungsbestrebungen. Um Unternehmen mit unterschiedlichen digitalen Reifegrad gleichermaßen zu unterstützen, wurden in der Ausschreibung gezielt zwei Schwerpunkte gesetzt“, erläutert Wirtschafts- und Forschungsreferent LH-Stv. Dr. Strugl. Die gezielte Forschungsförderung ist ein zentrales innovationspolitisches Instrument. Im Rahmen der Digitalisierungsausschreibung fördert das Land OÖ 14 innovative Forschungsprojekte mit einem Gesamtfördervolumen von insgesamt 5,68 Mio. Euro.
‚DigiFIT‘ erleichtert Start in Richtung Digitalisierung
„Der Ausschreibungsschwerpunkt ‚DigiFIT‘ soll es insbesondere produzierenden Unternehmen erleichtern, bestehende Hürden beim Start in Richtung Digitalisierung zu überwinden. Oft ist es der Fall, dass in der Vergangenheit hohe Investitionen in Fertigungsanlagen und -infrastruktur getätigt wurden, die nicht für die Digitalisierung gerüstet sind und aus wirtschaftlichen Gründen nicht einfach abgelöst werden können. Diese Unternehmen sollen dabei unterstützt werden, einen raschen Anschluss im Digitalen Wandel zu schaffen“, erklärt LH-Stv. Strugl. Zum Beispiel das Projekt „Universal Data Bridge für IoT-Anwendungen“ unter der Leitung von der abatec group AG adressiert dieses Thema mit der Entwicklung eines universell einsetzbaren Konnektivitätsmodul, um bestehende Anlagen und Geräte für die Digitalisierung aufrüsten zu können. Gesamt werden im Bereich ‚DigiFIT‘ 4 Projekte mit einem Volumen von 1,26 Mio. Euro gefördert. Das entspricht in etwa einem Viertel der Fördergelder.
‚DigiVALUE‘ steigert wertschöpfende Nutzung von Daten
„Mit ‚DigiVALUE‘ soll der Ausbau von Kompetenzen im Bereich der wertschöpfenden Nutzung von Daten massiv beschleunigt werden“, so LH-Stv. Strugl. Insgesamt fließen 4,42 Mio. Euro Fördermittel in 10 Innovationsvorhaben im Bereich ‚DigiVALUE‘. Vorausschauende Instandhaltung (Predictive Maintenance) von Produktionsanlagen und intelligente Vorhersagemodelle (Predictive Analytics) zur Optimierung von Produktionsprozessen unter Berücksichtigung von variablen Faktoren (wie z.B. Materialqualität, Leistung der Anlagen, Wetterbedingungen, uvm.) sind verstärkt wichtige Werttreiber in der Industrie und elementare Bausteine in der Industrie 4.0-Umgebung. Allgemein gilt es dabei, Entscheidungs- und Produktionsprozesse hinsichtlich Produktivität, Effizienz und Kosten weitgehend zu optimieren. Diese Aspekte finden sich in vielen ‚DigiVALUE‘-Projekten in den unterschiedlichsten Industriesegmenten. Die Beteiligung von vielen renommierten Industriebetrieben (wie Engel Austria, Fronius, Greiner Packaging, FACC Operations und viele mehr) zeigt, dass insbesondere in großen Industriebetrieben in diesem Bereich noch viel Potenzial zu heben ist.
Digitalisierung auch zentrales Thema für KMUs
Dass Digitalisierung und Industrie 4.0 nicht nur große Industriebetriebe betrifft, sondern auch Klein- und Mittelbetrieben enormes Potenzial bietet, zeigt sich an derhohen Beteiligung von KMUs. Insgesamt sind 15 Klein- bis Mittelbetriebe an den Projekten beteiligt, die rund 2/3 der Fördermittel im Unternehmensbereich einholen konnten. Im Bereich ‚DigiFIT‘ werden 3 der 4 Projekte von Klein- und Mittelbetrieben geleitet. Mit frischen Ideen sowie der Entwicklung von innovativen Technologien und neuartigen Geschäftsmodellen öffnen KMU-Betriebe oft neue Türen in die digitale Zukunft und sind oftmals Wegbereiter bzw. -begleiter für Industriebetriebe in der Digitalen Transformation. Zum Beispiel werden im Projekt ‚DiCoIN‘ (Digitally Connected Industry Network) unter der Leitung von SATIAMO GmbH Technologien entwickelt, um alle Akteure im Materialbeschaffungsprozess (wie Industriebetriebe, Zulieferer, Transportpartner) intensiv miteinander zu vernetzen. Für die Industriebetriebe bedeutet das effizientere Prozesse, geringere Kosten und optimierte Transportwege. An diesem Projekt ist u.a. auch die FH OÖ Entwicklungs & Forschungs GmbH beteiligt, die insgesamt bei der Ausschreibung einen großen Erfolg erzielen konnte. Die FH OÖ Entwicklungs & Forschungs GmbH leitet 6 der geförderten Projekte, ist an3 weiteren Entwicklungsvorhaben beteiligt und konnte insgesamt 1,78 Mio. Euro Fördermittel einholen.
Erste Ausschreibung im Rahmen von „STAR“
Die regionale Ausschreibung wurde im Rahmen des Strategischen Wirtschafts- und Forschungsprogramms ‚Innovatives OÖ 2020‘ initiiert und mit Mitteln der neuen Forschungsförderung STAR (Step Ahead through Research) finanziert. Der Call war die erste Initiative im Rahmen von STAR – insgesamt sollen zusätzliche 40 Mio. Euro in den Jahren 2017 – 2021 in die Forschungsförderung investiert werden. Die Konzeption wurde durch die Upper Austrian Research GmbH, die Forschungsleitgesellschaft des Landes OÖ, begleitet. Abgewickelt wurde die Ausschreibung in bewährter Weise durch die Österreichische Forschungsförderungsgesellschaft (FFG).
Mag.aDr.inHenrietta EGERTH - Geschäftsführerin FFG
Fortsetzung einer erfolgreichen Kooperation
Zwischen der Österreichischen Forschungsförderungsgesellschaft (FFG) und dem Land Oberösterreich gibt es eine langjährige, sehr erfolgreiche Kooperation. In den letzten Jahren hat die FFG für das Land OÖ bereits drei weitere Förderausschreibungen zu den Themen Medizintechnik, Produktionsstandort 2050 und Smart Mobility abgewickelt. Auch die aktuelle Ausschreibung zum Thema Digitalisierung wurde in bewährter Weise von der FFG umgesetzt.
„Informations- und Kommunikationstechnologien (IKT) sind heute nicht nur der ‚Lebensnerv der Wirtschaft‘, sondern durchdringen alle gesellschaftlichen und privaten Lebensbereiche. Aktuelle Themen reichen von der Bioinformatik, über Big Data bis hin zum Internet of Things, Industrie 4.0 und dem autonomen Fahren. Die Ausschreibung des Landes OÖ ist zu nationalen Förderprogrammen rund um das Thema Digitalisierung ergänzend. Bundesweite Programme decken zwar durch ihre inhaltliche Breite viele Themengebiete ab, die regionale Ausschreibung soll allerdings zusätzliche Dynamik in den für Oberösterreich zentralen Kernbereichen schaffen. Und Oberösterreich ist sehr erfolgreich darin, FFG-Fördermittel abzuholen“,erklärt Mag.a Dr.inHenrietta Egerth. 2016 konnte OÖ 103 Mio. Euro Bundesmittel (rund 1/5 der Gesamtfördermittel) ins Land holen und liegt damit an dritter Stelle hinter Wien und Steiermark. 86 % der Fördermittel gingen dabei an den Unternehmensbereich.
Das Land Oberösterreich setzt auf einer guten technologischen Basis und starken Kernkompetenzen in der produzierenden Industrie auf. In den Bereichen ‚Industrielle Fertigung‘ und ‚Werkstofftechnik‘ konnte OÖ in den Jahren 2014-2016 rund 40 % der bundesweit vergebenen Mittel ins Land holen. Auch im Rahmen des FFG-Basisprogramms lukriert OÖ durchschnittlich 80 Mio. Euro Fördermittel im Jahr (Durchschnitt 2006-2016) und liegt damit im Bundesländervergleich auf Platz 1.
Martin SCHWAIGER – SATIAMO
‚Digitally Connected Industry Network‘ bringt
hocheffiziente Materialbeschaffungsprozesse für die Industrie
Im Zeitalter der Digitalisierung sieht die Realität oft noch so aus, dass viele Industriebetriebe Bestellungen und Aufträge an Ihre Zulieferer und Transportpartner häufig noch manuell via E-Mail, Fax oder übers Telefon vergeben. Bei diesen Abläufen werden Probleme und Lieferverzögerungen aufgrund fehlender enger Vernetzung erst sehr spät erkannt. Das kann in den schlimmsten Fällen zu kompletten Produktionsausfällen führen. Hier setzt das Projekt DiCoIN – Digitally Connected Industrial Network, das sich zum Ziel gesetzt hat industrielle Wertschöpfungsnetzwerke weitgehend zu digitalisieren, an.
Industrielle Wertschöpfung spielt sich zunehmend in digitalen Netzwerken ab
Abläufe und Prozesse von industriellen Wertschöpfungsketten finden in zunehmenden Maßen in komplexen, vielschichtigen und globalen Netzwerken statt. An diesen Netzwerken sind hunderte unterschiedliche Unternehmen beteiligt – darunter Industriebetriebe, deren Zulieferer sowie Transportpartner. Diese Netzwerke sollen in erster Linie den Austausch von Daten und Informationen intensivieren, eine aussagekräftige Entscheidungsunterstützung bieten und die Möglichkeit schaffen, Prozessabläufe zu automatisieren. „Die Koordination solcher Netzwerke ist hochkomplex, da Materialbedarfe, Lieferzeiten und Lieferverfügbarkeiten sowie Transportkapazitäten in Einklang gebracht werden müssen, ohne dabei das Ziel aus den Augen zu verlieren, die eigene Prozesssicherheit angesichts auftretender Störungen und Engpässe sicherzustellen“, fasst Projektleiter Martin Schwaiger von SATIAMO die Herausforderung zusammen.
Projektpartner bringen viel Know-how aus der Praxis und Wissenschaft mit
Die beiden oberösterreichischen Start-Up-Unternehmen der IKT-Branche SATIAMO und curecomp sind in diesem Prozess schon weit voraus: Mit ihren Transportmanagement- sowie Lieferantenplattformen vernetzen sie schon jetzt hunderte Lieferanten und Transportpartner mit Industriebetrieben und vereinfachen durch diese „Digitalisierung“ die Abläufe. Beide Plattformen, sowohl die Transportmanagementplattform von SATIAMO als auch die Lieferantenplattform von curecomp, sind unabhängig voneinander bereits international erfolgreich. Gemeinsam mit oö. Forschungseinrichtungen der Johannes Kepler Universität Linz sowie der Fachhochschule Oberösterreich treiben die SATIAMO und curecomp den Entwicklungsprozess weiter voran. Dabei soll der bestehende Leistungsumfang beider Plattformen verknüpft und um neue digitale Services sowie innovative Automatisierungs- und Entscheidungsunterstützungs-ansätze erweitert werden.
Was für SATIAMO und curecomp einen strategisch wichtigen Ausbau des Leistungsportfolios bedeutet, kann für die industriellen Anwender Produktivitätsgewinne und Prozesssicherheit in bestehenden Abläufen bringen. Ob dem so ist, soll gemeinsam mit vier ausgewählten oberösterreichischen Leitbetrieben und Partnern aus unterschiedlichen Branchen (Banner Batterien, Donau Kanol, FACC und Fronius) anhand der im Projekt zu realisierenden experimentellen Prototypen untersucht werden.
Thematisch wird das bestehende Leistungsportfolio beider IKT-Partner um vier Innovationsfelder (Datenstandards, Automatisierung, Predictive Analytics und Multimediales) erweitert und zu einem Gesamtmodell eines digitalisierten, produktionsunterstützenden Materialbereitstellungsprozesses ausgebaut: Es sollen digitale Lieferscheine erstellt werden, die in einem zweiten Schritt die Ausgangsbasis für den automatisierten Transportabwicklungsprozess sind. Mittels Predictive Analytics soll darauf aufbauend ein risikobasiertes Prozesscontrolling des Materialbereitstellungsprozesses aufgesetzt werden, das sicherstellt, dass Prozess- und Lieferzeiten eingehalten werden; wenn überhaupt, soll der Mensch nur noch auf Basis „Management by Exception“ in den Prozess eingreifen.
Zuletzt soll auch die Qualitätssicherung im Prozess multimedial unterstützt werden. So kann etwa eine Reklamation über eine Smartphone-App erstellt und bearbeitet werden. Damit trägt das Projekt nicht nur zu einer realen Digitalisierung und gleichzeitigen Produktivitätssteigerung bei den Anwendern bei, es gewährleistet zukünftig die Prozesssicherheit zu einem Bruchteil der bisherigen Prozess- und Transaktionskosten.
DI Dr. Gerhard DIMMLER – Engel Austria GmbH
Virtueller Produktionsassistent (VPA 4.0) soll
Qualität und Effizienz in der Produktion weiter steigern
Im Zeitalter von Industrie 4.0 sind Prozess- und Maschinendaten zunehmend ein ganz wesentlicher Teil der Wertschöpfung eines produzierenden Unternehmens. Viele Unternehmen haben mit ihren Digitalisierungsinitiativen die Basis gelegt, umfangreiche Datenmengen automatisiert zu erfassen. Die nutzenbringende Aufbereitung dieser enormen Datenmengen bringt allerdings noch große und vielfältige Herausforderungen mit sich. Aus diesen großen Datenmengen sollen:
· Echtzeitinformationen gewonnen werden, die es erlauben, sofort auf kurzfristige Änderungen in der Produktion zu reagieren (Adaptive Production),
· aussagekräftige Informationen gewonnen werden, die es ermöglichen, zukünftige Einflüsse auf die Produktion genau zu prognostizieren (Predictive Production) und
· vor allem zielgerichtete Informationen über den Zustand der Anlagen und Komponenten in der Produktion erhalten werden (Predictive und Preventive Maintenance).
Die RISC Software GmbH stellt sich der Herausforderung, im Rahmen des grundlagennahen Forschungsprojekts ‚VPA 4.0 – Virtueller Produktionsassistent‘ aus den großen Datenströmen – verknüpft mit den Modelinformationen von Maschinen und Prozessen – ein verbessertes Verständnis und eine ganzheitliche Betrachtung der Produktionsanlagen zu generieren. Gemeinsam mit den oberösterreichischen Maschinenbauunternehmen ENGEL AUSTRIA GmbH und FILL Gesellschaft m.b.H. werden die gewonnen Erkenntnisse bzgl. Datenaufbereitung und Datenanalyse anhand von Praxisszenarien in den Bereichen Produktion und Instandhaltung evaluiert.
Durch die Verknüpfung und intelligente Aufbereitung von Echtzeitinformationen aus der Produktion (wie z.B. Werkzeug-, Maschinen-, Prozess- und Konfigurationsdaten) mit Daten aus den Geschäftsprozessen (wie z.B. Auftragsdaten aus den ERP-Systemen oder Produktionsdaten aus den MES-Systemen) werden Informationen zur domainübergreifenden Produktionsoptimierung abgeleitet. Ziel ist es, ein besseres Verständnis der gesamten Produktionsanlagen bzw. des Maschinenparks zu gewinnen. Um die unterschiedlichsten Datenströme aus der Produktion und den Geschäftsprozessen zu verknüpfen, soll ein hybrides Datenbanksystem erstellt und die Daten in diesem zusammengeführt werden. Die gleichen Herausforderungen gilt es, für das Thema ‚Preventive und Predictive Maintenance‘ zu lösen. Aus Maschinen- und Anlagenbausicht gibt es jedoch einen wesentlichen Unterschied. In der Instandhaltung bestehen die Datenströme vor allem aus Maschinendaten, die in den meisten Fällen firmenübergreifend ausgetauscht werden müssen, um sie entsprechend interpretieren zu können.
Ungeachtet der Datennutzung ermöglicht eine homogene Datenbasis somit die Anwendung von semantischen Datenmodellen, um das Fachwissen von Experten/innen sowohl aus der Produktion und Instandhaltung als auch von den Herstellern der Anlagen und Maschinen abzubilden. In der Kombination mit physikalischen Beziehungen ermöglicht dieses Fachwissen ein digitales Abbild der Produktionsanlagen und legt den Grundstein für die Weiterverarbeitung mit Methoden der Anomalie- und Ausreißerkennung, weiteren Analysemethoden zur Erkennung von Mustern und Zusammenhängen bis hin zum Einsatz künstlicher Intelligenz.
Der virtuelle Produktionsassistent (VPA 4.0) unterstützt die Experten/innen bei der Datenauswertung und sorgt durch visuelle Darstellungen für ein wesentlich besseres Verständnis der gesamten Produktionskette. Dabei wird die Komplexität der immer größer werdenden Datenmengen in den automatisierten Produktionsprozessen reduziert. Gleichzeitig bietet der VPA 4.0 den Experten/innen eine fundierte Entscheidungsgrundlage, um die Wartungsintervalle zu reduzieren und die Qualität des Produktionsergebnisses zu erhöhen.
Rückfragen:
Michael Herb MSc, Presse LH-Stv. Strugl,
Tel. 0732/7720-15103 oder 0664/6007215103
Mag. (FH) Gerlinde Tuscher, FFG,
Tel. 05 7755 6010 oder 0664/8569028
Petra Mayer-Hejna, MSc, UAR,
Tel. 0732/9015-5637 oder 0664/9658926
Kontakt
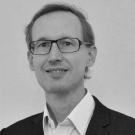